Troubleshooting Your Ice Machine
As a manager, you know how important it is to keep your guests happy. One essential component is ensuring that your ice machine is working properly at all times. However, like any piece of equipment, ice machines can experience issues from time to time. In this blog post, we will provide you with a comprehensive guide on troubleshooting common problems with your ice machine and when it may be necessary to call an HVAC professional.
Ice Machine Not Producing Ice
One of the most common issues managers face with their ice machines is when they stop producing ice altogether. The first step in troubleshooting this problem is to check the water supply to the machine. Make sure that the water line is connected properly and that there are no blockages preventing water from reaching the machine. If the water supply seems fine, the next step is to check the condenser coils for dust and debris. Dirty condenser coils can prevent proper cooling and lead to a decrease in ice production.
Ice Machine Producing Thin or Hollow Ice
If your ice machine is producing thin or hollow ice cubes, it could be a sign of a problem with the water level sensor or the evaporator plate. Start by checking the water level sensor to ensure it is functioning correctly and that it is set at the right level. If the sensor appears to be working fine, then you may need to inspect the evaporator plate for any damage or buildup of mineral deposits. Cleaning or replacing these components may help resolve the issue and improve ice quality.
Ice Machine Making Loud Noises
Another common issue manager’s encounter with their ice machines is unusual noises coming from the unit. These noises can range from loud banging sounds to high-pitched squealing noises. In most cases, loud noises indicate a problem with one of the internal components, such as a faulty motor or compressor. It is crucial not to ignore these noises as they can lead to more significant issues if left unaddressed. Contacting Environmental Air Systems promptly can help identify and resolve the source of the noise before it causes further damage.
Ice Machine Leaking Water
If you notice water leaking from your ice machine, it is essential to address this issue promptly to prevent damage to surrounding areas and potential safety hazards for guests and staff. Begin by checking for any visible leaks around the water lines or connections leading into and out of the machine. Tightening loose connections or replacing damaged parts may solve minor leaks; however, if water continues to leak after addressing these issues, it may be best to seek assistance from Environmental Air Systems. We can diagnose and often repair more complex leaks within the unit.
When To Call an HVAC Professional
While some minor issues with your ice machine can be resolved with simple troubleshooting steps, there are instances where calling Environmental Air Systems becomes necessary. If you have attempted several troubleshooting methods without success or if you are unsure about how to proceed safely, do not hesitate to contact a qualified technician for assistance. In either case, an experienced HVAC professional like Environmental Air Systems will have the specialized knowledge and tools needed to diagnose complex problems accurately and implement effective solutions efficiently. In addition, regular maintenance programs that we offer are also very, very important. These ensure that the systems are checked, coils are clean, and the system components are operating efficiently. This in turn means less down time and/or emergencies, fewer major repairs, and longer lasting (expensive) equipment.
Maintaining a fully functional ice machine is crucial for ensuring guest satisfaction and operational efficiency within your establishment. Remember to prioritize regular maintenance checks on your ice machine as prevention is key to avoiding costly repairs down the road.
When you need help with your ice machine, contact us at Environmental Air Systems Inc.
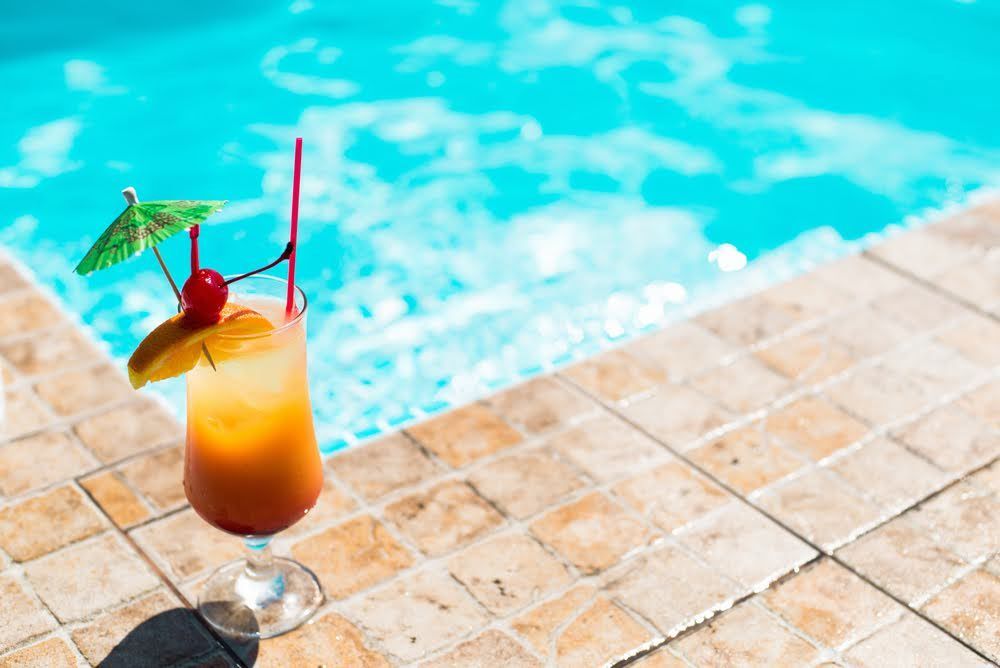